Every industry in the world today is moving towards the digitization of its supply chains. The reason is fairly simple – no one wants to be left behind using soon-to-be obsolete methods and ways of working. The automotive industry is no exception to this notion being at the forefront of digitizing their supply chain models while moving towards sustainable mobility solutions. Several academicians have reviewed, analyzed, and brought about various studies on sustainable supply chains within the automotive industry. From raw material procurement to manufacturing and sales, there are so many processes that are involved in the making of an automobile and it is easy to forget the intricacies involved in sustainable sourcing and usage of these materials.
Understanding the Problem
Traditional supply chains have an urgent need to transform into inter-connected, smart, and efficient ecosystems to run customer solutions and digital operations hand in hand. This would provide the company to effectively cater to customers in a faster way by quickly identifying changes in demand and organizing supply chain activities accordingly. With evolving systems, there exists a looming question about the sustainability of digitizing systems and moving towards electrification of systems.
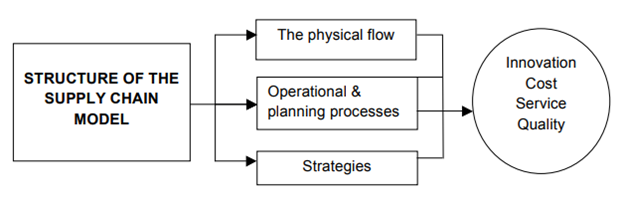
Of course, there exists both challenges and opportunities while moving towards data-driven sustainable supply chain practices. Based on various studies done within the field, I go out on a limb to say that the only way to say that the development of big data analytics has become synonymous with building a competitive sustainable supply chain and the impact it has on the economic, environmental, and social paradigms of indicators further strengthen my claim. (Manzetti & Mariasiu, 2015) This necessity has brought about companies and governments working together in their efforts to tackle climate change and bring about a successful sustainable transformation.
Sustainable Development and Electrification
Many studies have talked about the environmental and economic benefits of moving forward with the complete electrification of automobiles. But the social paradigm has been heavily neglected from the perspective of automotive industry development, and the United Nations’ 2030 agenda for sustainable development involves the 17 Sustainable Development Goals (SDGs) to be addressed and followed. When we take into consideration the automotive industry, the entire value chain with a variety of subprocesses needs to be abstracted and viewed from a bigger perspective.
Europe is seen to be at forefront of technological innovations in driving sustainable growth towards supply chain management, and the types of vehicles now in production are traditional fuel-based vehicles, full hybrid, plug-in hybrid, and electric vehicles (Günther, et al., 2015). Let us take the example of one of the biggest transformative industries in the Swedish landscape, Volvo Cars. The company’s ambition is to be completely climate-neutral across its value chain by the year 2040 and has started taking major steps in that respective direction. Right now, in their pipeline, all the cars are either plug-in hybrids or fully electric meaning that they are getting closer to their ambition for 2040 and essentially closing in on their 2025 goal of having 50% of the respective types of cars.
Recognizing an urgent need to digitize systems and change course in line with the climate change imperatives discussed at the Paris Agreement calls for our attention. Not only Volvo cars, but other European manufacturers like Renault, Audi, BMW, and Volkswagen are moving towards electric powertrain components and incorporating AI in machines along with it. So, the bottom line is to understand that with changing times that call for improved machines, the processes change accordingly – from raw material procurement to processing. Let us not stop with car manufacturers and expand the scope of trucks, buses, and other automotive which are being a part of the electrification.
How are automotive firms approaching this changing landscape?
Pre-Covid, companies had a set roadmap in place to achieve certain targets by 2020 to start the new decade with promising results. But since the onset of the virus, it has been a setback for firms and the automotive industry is looking to rev up production volumes and reinforce relationships with their suppliers whose businesses took a hit during the lockdown phase in many parts of the world.
Given the current world situation of how climate change is to be tackled at a raging pace and rising consumer demands need to be met at the same time brings us to the crossroads of how big data helps in demand forecasting, and how the electrification of vehicles has an effect of the entire supply chain. It is a complex topic at hand to discuss, and for that reason, specific questions are addressed in this study.
● How does electrification of the automotive industry affect sustainability in supply chains?
● How can demand forecasting tools change the field of the automotive sector?
To address these questions, the concepts surrounding demand and inventory planning, big data predictive analysis, and electrification of industries need to be considered. The future mobility challenge can be understood by looking at what big firms within Europe are doing, and by conversing with professionals in the industry. In the next section, the relevant literature used in this study is briefly reviewed and the following section after that ideally talks about the industrial supply chain now and before, and the model that is changing now. Electric vehicle battery technologies are associated with green technologies, which reduce the carbon impact on the environment. When I think about Industry 4.0, I take a step back and ponder upon the usage of battery technologies, operational excellence, and reverse logistics.
Sustainable Supply Chains (SSCs)
We constantly talk about Sustainable Supply Chains (SSCs) being the way forward in an industrial landscape irrespective of the type of business. The convergence of various perspectives on sustainability lies in understanding the underlying aspect of the Triple Bottom Line (TBL) Theory. Sustainable Supply Chain Management is a concept that was born out of concerns regarding the paradigms involved in the triple bottom line theory, and firms have long since started to incorporate sustainability reports documenting their activities relating to their operational, and sourcing practices to drive transparency and trust amongst their key stakeholders.

Importantly, four key indicators stand out when defining sustainability in terms of supply chain management and they are strategy, risk management, organizational culture, and transparency. Now, automotive supply chains have the most complex of processes when it comes to dealing with sustainability issues. In the last decade, the automotive industry has been seeing a transcendence in terms of technological innovations, and with new technologies in place, comes new challenges.
Automotive Supply Chains & Challenges
In a typical industrial landscape, we can see the raw materials being sourced from the supplier to the Original Equipment Manufacturers (OEMs) via multiple modes and channels, after which it eventually reaches the market and then to the consumer. Like any other supply chain system, it involves forward flows, reverse flows, and so on. In general, a car has about 10,000 moving parts and can have so many variants within the same modular structure and design and within automotive industries, the main sources to look at for supply chain activity is the raw material procurement location, production capacity and place, and the extended market reach. The geographical areas that are powerhouses in terms of homes to automotive industries and suppliers are North West, South West, and Eastern Europe within the European Union and North America within the Americas. The trade-offs that happen in the actual scenario of a supply chain are found to be massive in terms of complacency in either economic or environmental factors to cater to the societal norms and practices, and these are being radicalized and changed with the electrification of the mobility sector (Kannegiesser & Günther, 2014).
A Changing Landscape
In a typical industrial landscape, we can see the raw materials being sourced from the supplier to the Original Equipment Manufacturers (OEMs) via multiple modes and channels, after which it eventually reaches the market and then to the consumer. Like any other supply chain system, it involves forward flows, reverse flows, and so on. In general, a car has about 10,000 moving parts and can have so many variants within the same modular structure and design and within automotive industries, the main sources to look at for supply chain activity is the raw material procurement location, production capacity and place, and the extended market reach. The geographical areas that are powerhouses in terms of homes to automotive industries and suppliers are North West, South West, and Eastern Europe within the European Union and North America within the Americas. The trade-offs that happen in the actual scenario of a supply chain are found to be massive in terms of complacency in either economic or environmental factors to cater to the societal norms and practices, and these are being radicalized and changed with the electrification of the mobility sector (Kannegiesser & Günther, 2014).
A Changing Landscape
Electrification of systems and vehicular infrastructure came along with a lot of perks, and it had a fair share of challenges to look for, too. There are many dynamic elements when considering sustainable supply chains 10 years from now with the development of advanced powertrain systems and extensive fleets of electric vehicles in the future. The ultimate attempt is happening right now as we speak in countries with major automotive presence such as Germany, Netherlands, Sweden, etc., with the development of hybrid powertrains and fully electric models. In addition to this, the government of the EU supports in a major way with incentive programs in place for electric vehicles. Now, several authors have proposed various frameworks regarding sustainable supply chains within the automotive industry. Different activities take place within the supply chain and some activities can be grouped as forwarding supply chain, reverse supply chain, and energy supply chain as the figure below represents. Automotive OEMs and part manufacturers have combined their lean ways of working with actionable machine learning capabilities to assist them with demand planning and inventory control. Not only that, the Artificial Intelligence capabilities that firms showcase concerning sourcing maps out end-to-end compliance control in regards to sustainable sourcing and usage of non-conflict minerals and other materials.
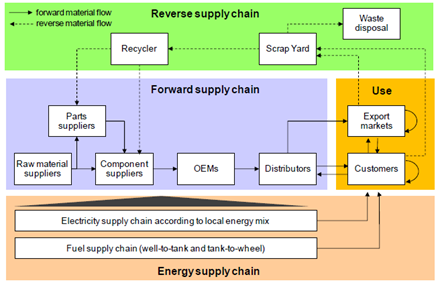
Source: (Günther et al., 2015)
Sustainability optimization is dependent on certain key performance indicators that each department within the firm has in place and strategies that are in place within the integrated value chain model. With the number of vehicles sold every year growing at an unprecedented level, we know that consumer demands would play a major role in an optimized supply chain network. People are starting to get educated on the different aspects of sustainable living and sustainable transport especially in Europe, and this has led to a faster adoption rate of electric vehicles with battery-loaded powertrains in place.
Vehicle components are highly variable depending on the type of powertrain used. The vehicle type ranges from a) conventional vehicle, b) fully hybrid vehicle, c) plug-in hybrids, and d) battery electric vehicle. With the statistic showing that the electric fleet of vehicles on the road to increase at an exponential level, it is fairly safe to say that the demand for battery systems would be high, but the cost reduction would be on a massive scale owing to the boom of electrification. One would wonder why that might be the case, but as we move toward a new world order, competition starts to build up for the booming business which is batteries, and eventually, prices would be on a decline. That being said, there are various types of batteries such as lead-acid, nickel-cadmium, lithium-ion, etc. The most commonly produced and commonly used in place now is the Lithium-Ion (Li-ion) batteries which have a very high energy capacity but have a limited life cycle (Manzetti and Mariasiu, 2015).
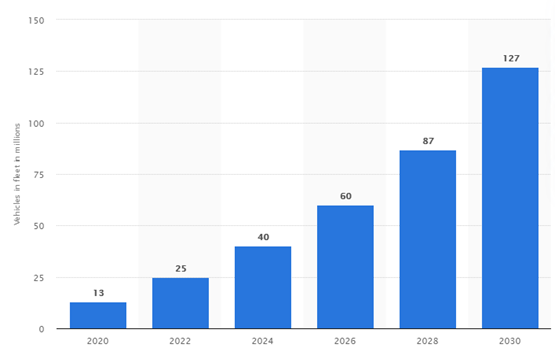
References
Carter, Craig R., and P. Liane Easton. 2011. “Sustainable Supply Chain Management: Evolution and Future Directions.” International Journal of Physical Distribution & Logistics Management. https://doi.org/10.1108/09600031111101420.
Günther, H-O, M. Kannegiesser, and N. Autenrieb. 2015. “The Role of Electric Vehicles for Supply Chain Sustainability in the Automotive Industry.” Journal of Cleaner Production. https://doi.org/10.1016/j.jclepro.2014.11.058.
Kannegiesser, M., and H-O Günther. 2014. “Sustainable Development of Global Supply Chains—part 1: Sustainability Optimization Framework.” Flexible Services and Manufacturing Journal. https://doi.org/10.1007/s10696-013-9176-5.
Manzetti, Sergio, and Florin Mariasiu. 2015. “Electric Vehicle Battery Technologies: From Present State to Future Systems.” Renewable and Sustainable Energy Reviews. https://doi.org/10.1016/j.rser.2015.07.010.